
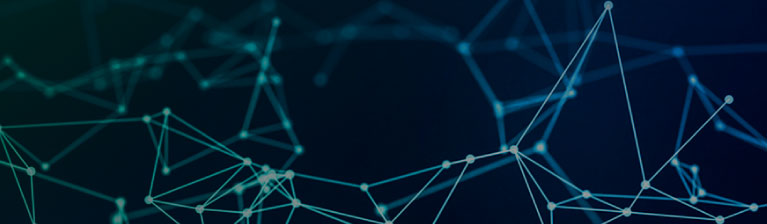
Negative electrode material
High performance negative electrode material
Rare earth-nickel AB5 hydrogen absorbing alloy is generally used as the negative electrode material for nickel-metal hydride batteries.
As shown in the figure, if storing 10L of hydrogen gas, the high-pressure gas cylinder needs 14.3cc, but the hydrogen absorbing alloy can store at a high density of 7.5cc.
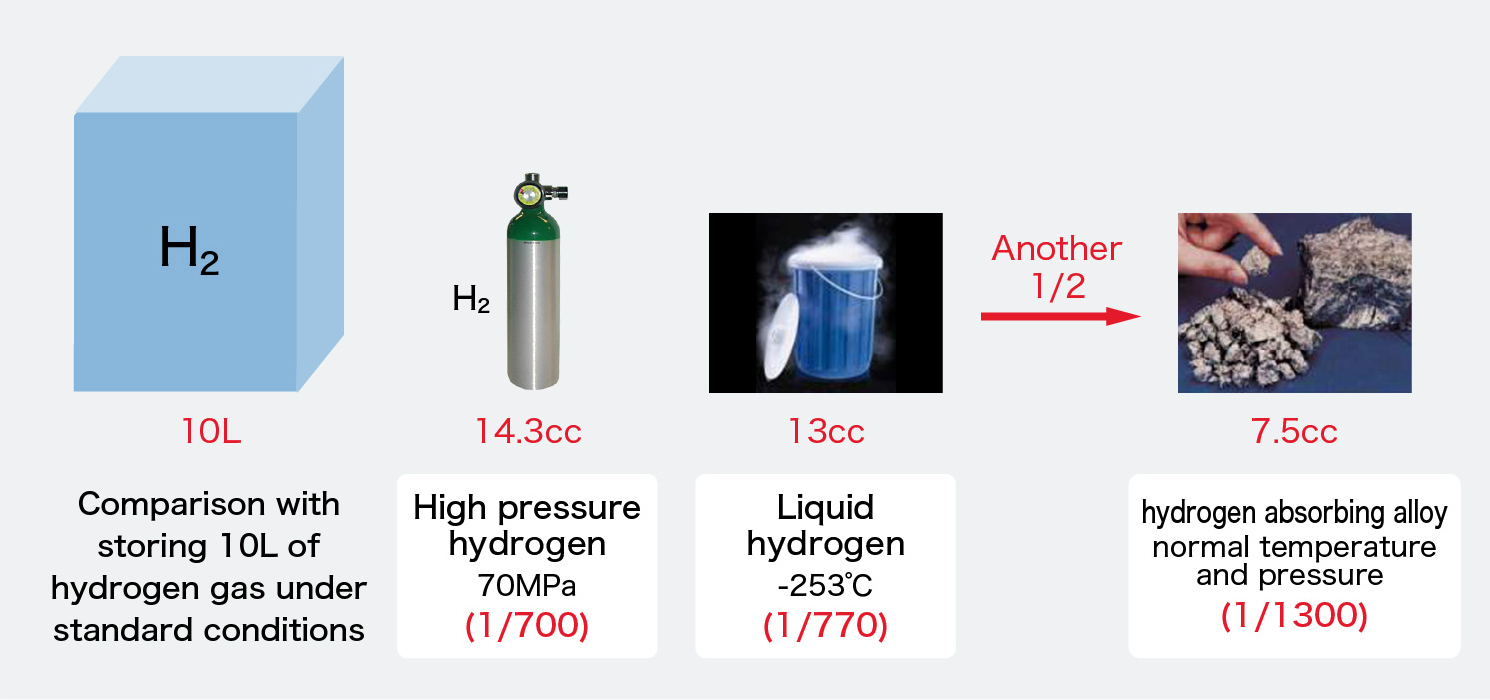
Comparison with storing 10L of hydrogen gas under standard conditions
FDK's original technology
FDK uses a rare earth-magnesium-based A2B7 type alloy called a "superlattice hydrogen absorbing alloy" instead of a rare earth-nickel-based AB5 type alloy as shown in the figure.
The features of our original superlattice hydrogen absorbing alloy are as follows.
The features of our original superlattice hydrogen absorbing alloy are as follows.
- A2B7 type crystal structure that has the merits of both AB2 type and AB5 types
- Achieves both high capacity and high corrosion resistance due to its unique crystal structure
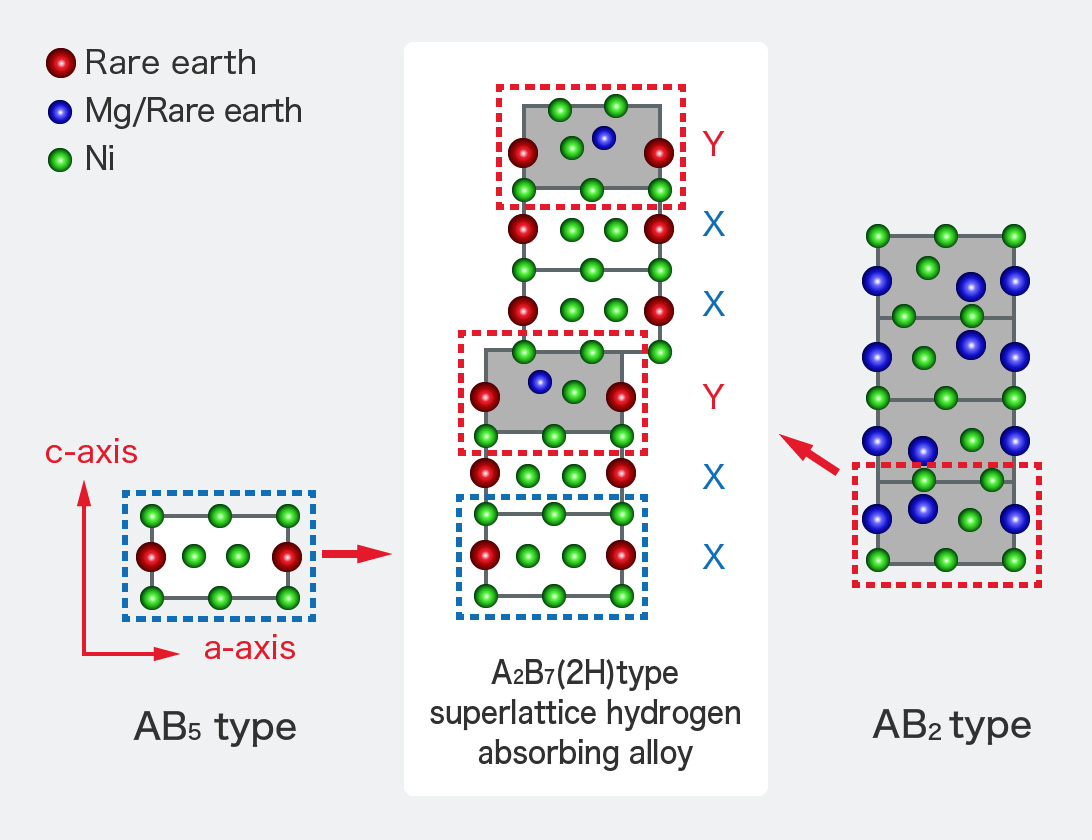
crystal structure | AB2 | ||
---|---|---|---|
AB2unit number | 1 | 1 | 0 |
AB5unit number | 0 | 2 | 1 |
Electrochemical capacity per volume | (△) | 〇 | × |
Alloy pulverization oxidation (corrosion) | 〇 | 〇 | × |
reversibility of hydrogen absorption | × | 〇 | ◎ |
cell life | × | ◎ | 〇 |
Introduction of sample analysis results at FDK
We have established the analytical material crystal structure techniques in cooperation with Fujitsu Laboratories Co., Ltd. and Kyoto University*1 , using a synchrotron radiation X-ray device such as SPring8, a scanning electron microscope (SEM) and transmission electron microscope (TEM).From these analysis results, we analysed the crystal structure of polyphasic, complex and superlattice hydrogen absorbing alloys and used them as guidelines for development.
※1:I.J. hydrogen Energy 42(11574-11583) 2017
Crystal structure analysis of superlattice hydrogen absorbing alloy (RE0.9Mg0.1Ni3.3Al0.2)
We analysed the crystal structure using synchrotron powder X-ray diffraction (XRD), and using Rietveld analysis of diffraction peaks to determine phase ratios and element occupancy sites.
R factor | Rwp | 4.36 | |
---|---|---|---|
Convergence value | S | 3.42 | |
Weight ratio of crystal structure | A2B7_2H | 91.2% | |
A2B7_3R | 1.7% | ||
A5B19_2H | 1.2% | ||
A5B19_3R | 3.5% | ||
AB5 | 2.4% | ||
A2B7_2H Element occupancy rate |
A site element | RE | Mg |
RE1(AB2) | |||
RE2(AB5) | 0.0% | ||
B site element | Ni | Al | |
98.5% | 1.5% | ||
boundary) |
81.4% | 18.6% | |
Ni3(AB5) | 95.7% | 4.3% | |
Ni4(AB5) | 100.0% | 0.0% | |
Ni5(AB5) | 94.5% | 5.5% |
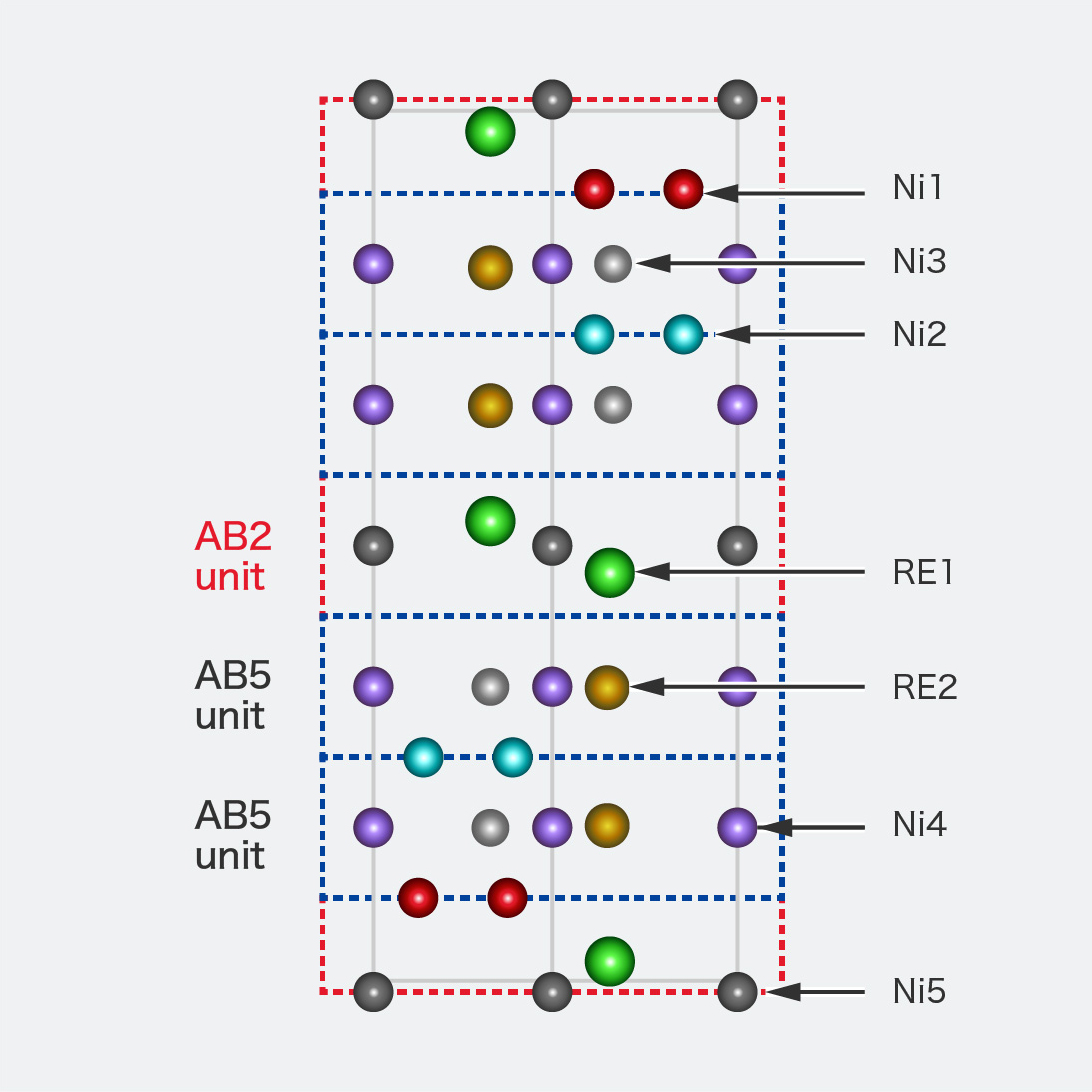
STEM images of superlattice hydrogen absorbing alloys (RE0.9Mg0.1Ni3.3Al0.2)
We directly observed the atomic arrangement of the alloy using STEM, and we confirmed consistency of XRD analysis results.
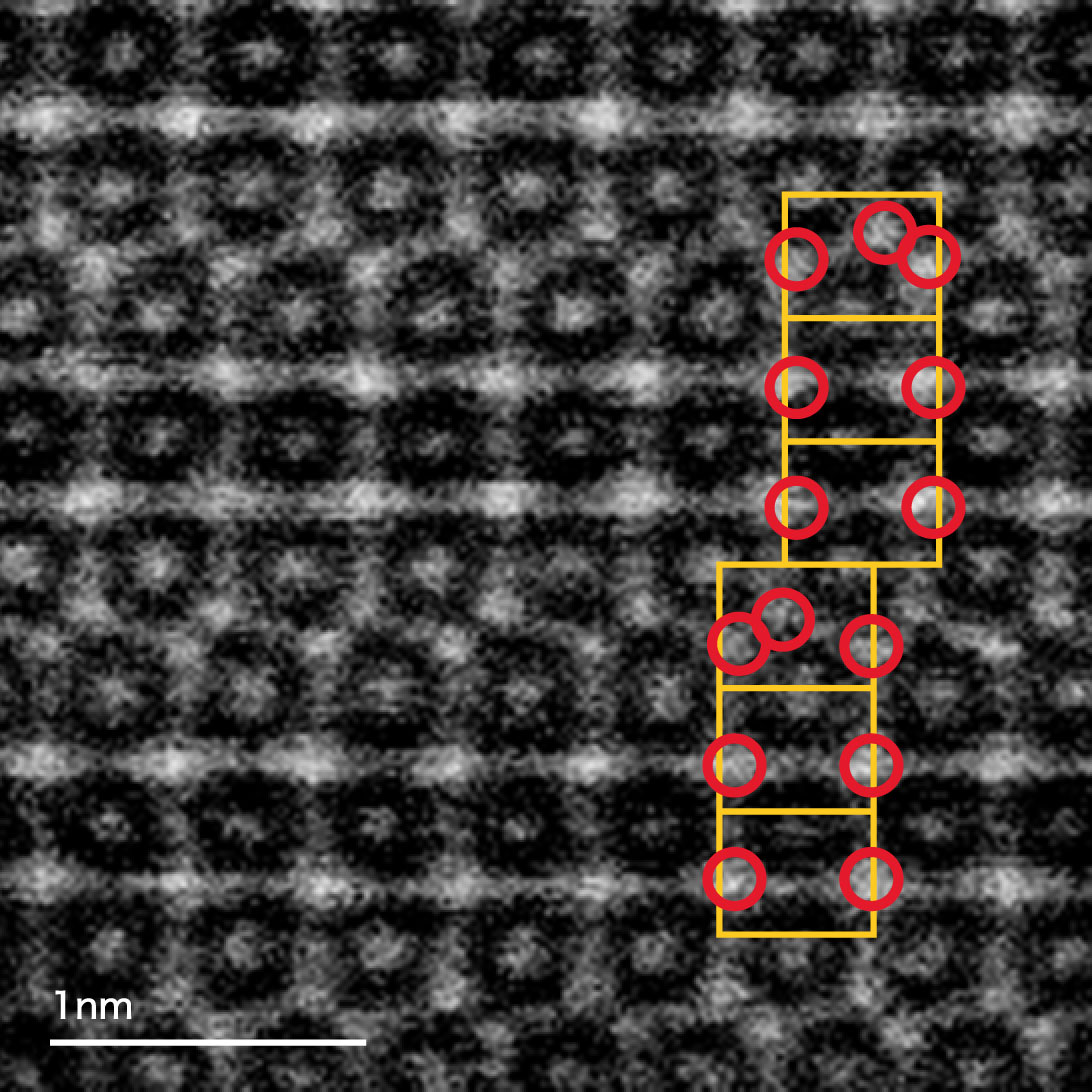
SEM image of the surface of the hydrogen storage alloy after cell charging and discharging
After cell charging and discharging, the surface of the hydrogen absorbing alloy is observed to confirm the corrosion state.
The main cause of deterioration of nickel-metal hydride batteries is the corrosion of the hydrogen absorbing alloy. We measured the magnetic susceptibility of the amount of metallic Ni and predicted the battery life from the level of corrosion (oxidation).
The main cause of deterioration of nickel-metal hydride batteries is the corrosion of the hydrogen absorbing alloy. We measured the magnetic susceptibility of the amount of metallic Ni and predicted the battery life from the level of corrosion (oxidation).
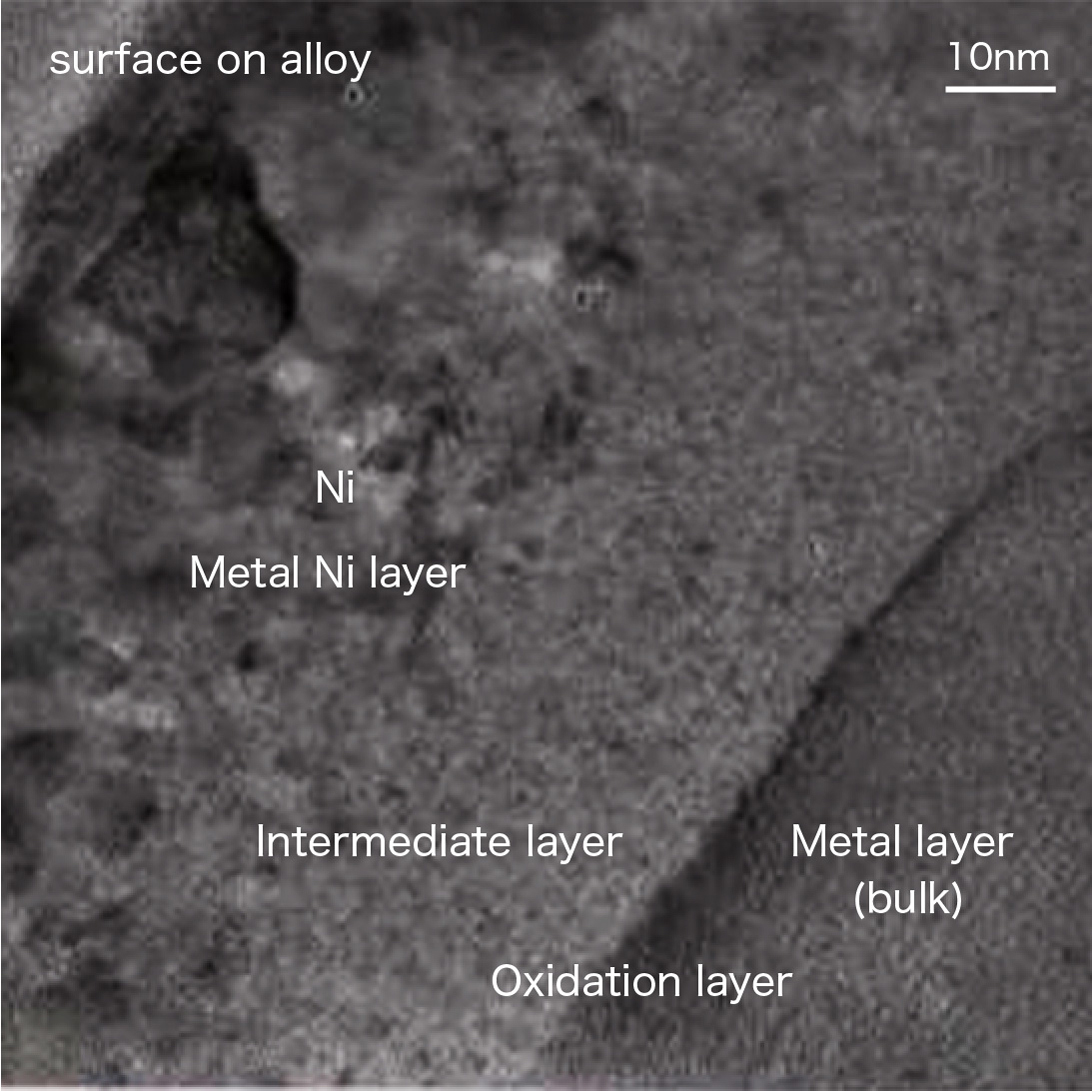